Service
We understand the critical importance of having reliable lifting equipment that complies with all regulatory requirements on a daily basis. According to local Occupational Health & Safety Administration guidelines, regular safety checks, including load tests for all types of cranes and hoists, are mandatory.
By choosing GMV for your annual inspections, you benefit from the expertise of qualified personnel with extensive experience. Following the inspection, we provide a detailed service report outlining all checks performed. Cranes and hoists receive a labeled certification indicating the date of inspection and load test.
If you are located outside GMV’s service area, you can contact one of our certified partners.
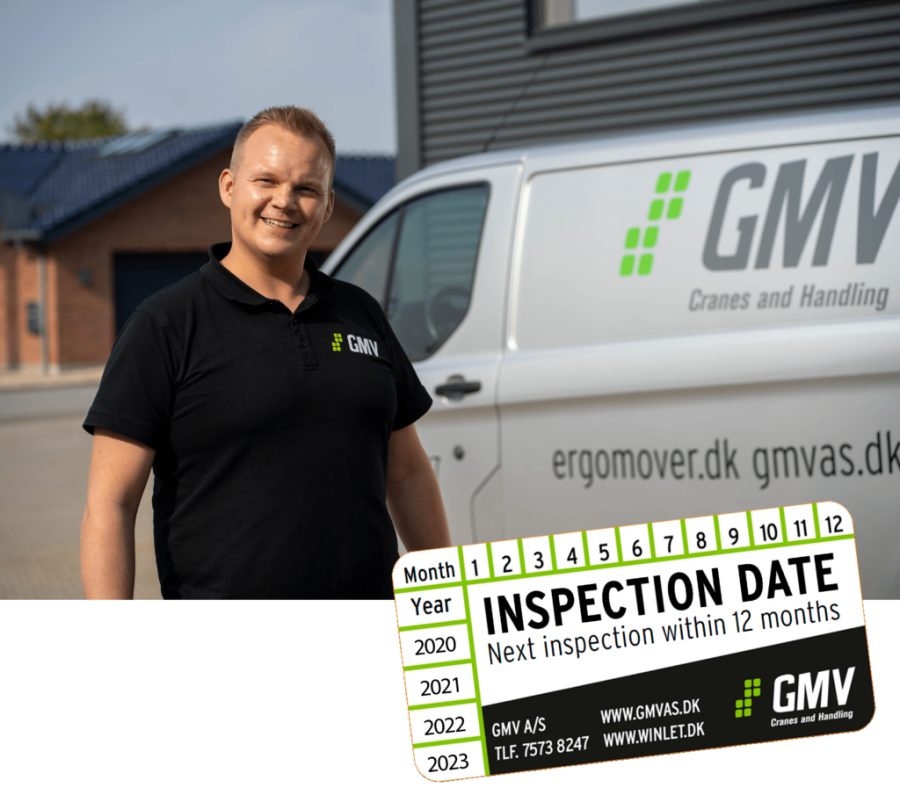
Service agreement
At GMV we offer a comprehensive service agreement to ensure that your lifting equipment operates flawlessly at all times.
- Our annual safety check meets all regulatory requirements and is conducted on schedule. This safety check covers all Winlet, ErgoMover and Handling products.
- The service agreement itself is free of charge, however, you are responsible for the startup fee, transportation costs, service technician labor hours and any necessary spare parts.
If you are located outside our service area, please contact us, and we will connect you with a trained partner nearby.
Fast delivery of spare parts
All spare parts are available for same-day shipping directly from our stock if the order is placed before 1 pm.
Service & remote support
We are always ready to assist if unforeseen issues arise with your lifting equipment. We offer repair services either at our factory or on-site, depending on your needs.
If you experience malfunctions or breakdowns during your daily operations, or encounter any other issues, we are available to provide support.
Additionally, we offer online remote support for all our Winlet glasslifters. This allows us to assist you by accessing the software installed on the machines and resolving issues remotely.
Training
We provide training to all our partners, offering a comprehensive overview of the technical specifications and general operation of our equipment.